V avtomobilski industriji so proizvajalci originalne opreme v preteklosti večinoma uporabljali aditivno proizvodnjo za hitro izdelavo prototipov. V zadnjih letih pa napredek na področju aditivne proizvodnje počasi spreminja načine oblikovanja, izdelave in distribucije delov za končno uporabo. Deloittejeva 3D-priložnost v študiji avtomobilske industrije pojasnjuje, da podjetja na trenutni standardni poti aditivne proizvodnje ne iščejo radikalnih sprememb niti v dobavnih verigah niti v izdelkih. Aditivna proizvodnja je sprejeta kot orodje za ustvarjanje ponovitev oblikovalnih izdelkov, za izboljšanje kakovosti s stroškovno učinkovito izdelavo prototipov in ustvarjanje posebnih delov orodja. Kljub temu obstajajo druge poti aditivne proizvodnje v avtomobilski industriji, ki bolj radikalno preoblikujejo izdelke in dobavne verige. To bomo raziskali v sledečem pregledu vpliva aditivne proizvodnje v avtomobilski industriji. Dejansko je poročilo SmarTech Analysis pokazalo, da bo do leta 2029 3D-tisk v avtomobilski industriji ustvaril 9 milijard dolarjev prihodkov samo s proizvodnjo delov za končno uporabo, v primerjavi s 1,39 milijarde dolarjev v letu 2019. Kam torej vodi aditivna proizvodnja v tem sektorju?
Predprodukcijske koristi
Pospeševanje faze oblikovanja med razvojem novih izdelkov je ključno v kateri koli industriji. Na srečo lahko 3D-tisk v tej fazi nadomesti drago in dolgotrajno CNC proizvodnjo. Natančneje oblikovalcem omogoča, da stroškovno učinkovito opravijo več ponovitev, preden se odločijo za končni izdelek. Postopek je sledeč: ko oblikovalci ugotovijo potrebo uporabnika in ustvarijo ideje, da bi te potrebe zadovoljili, razvijejo prototip. Naslednja faza je preizkus tega prototipa, da bi izboljšali njegovo zasnovo. Ta ponavljajoči se proces imenujemo tudi hitro prototipiranje.
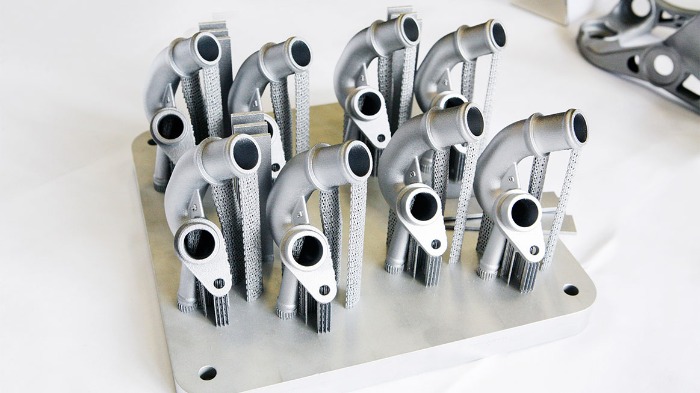
Vzorec kovinskih 3D-natisnjenih priključkov za vodo motorja Audi W12 | Vir fotografije: Volkswagen AG
Volkswagen se na primer zadnjih 25 let ukvarja s tehnologijami 3D-tiska. In ravno lani so investirali v dva dodatna Stratasys 3D-tiskalnika. Peter Bartels, vodja Volkswagnovega predserijskega centra, je komentiral, da te naložbe predstavljajo “dodatne zmogljivosti, ki krepijo operacije 3D-tiska in omogočajo dodatno optimizacijo procesa oblikovanja.” Poleg tega je mogoče optimizirati oblikovanje orodja (ročajev, vbodov in vpenjal) in ga izdelati po nižjih stroških. Orodje ima na montažni liniji pomembno vlogo pri proizvodnji ponavljajočih se in kakovostnih izdelkov. Te aplikacije so tisto, kar Deloitte imenuje trenutna standardna pot aditivne proizvodnje v avtomobilski industriji.
Rastoči segment delov za končno uporabo
Poleg tega se je več proizvajalcev originalne opreme zanimalo za 3D-tisk v razvoju delov za končno uporabo, ki presegajo hitre aplikacije za izdelavo prototipov. Za to obstaja veliko razlogov, ki jih lahko povzamemo, kot iskanje inovacij izdelkov v konkurenčnem sektorju, kot je avtomobilska industrija. Eden od načinov za doseganje inovativnosti izdelkov je dramatično povečanje učinkovitosti dela, na primer z zmanjšanjem njegove teže. Inovacije izdelkov s prilagajanjem so prav tako zelo zanimive, zlasti za proizvajalce luksuznih avtomobilov.
Dejansko je prednost uporabe aditivne proizvodnje potencialna proizvodnja sestavnih delov z manjšo težo za ustvarjanje vozil, ki porabijo manj goriva. Vloga programske opreme za industrijsko oblikovanje je tako osrednja. Z leti so se rešitve CAD in CAM drastično izboljšale, zlasti za aditivno proizvodnjo. Pogosto vključujejo orodja za generativno načrtovanje, optimizacijo topologije in ustvarjanje rešetk, ki zmanjšujejo skupno težo delov, hkrati pa ohranjajo ali izboljšujejo njihovo delovanje. Lažji deli so pogosto bolj zapleteni. Ker pa aditivna proizvodnja ni omejena z vidika svobode oblikovanja, za razliko od običajnih metod kompleksnost ne predstavlja izziva. Treba je opozoriti, da je poenostavitev delov možna tudi zaradi aditivne proizvodnje, s konsolidacijo več delov v enotno zasnovo. Zato bi se lahko kompleksnost sestavljanja dolgoročno zmanjšala, če bi bilo treba izdelati veliko količino teh delov.
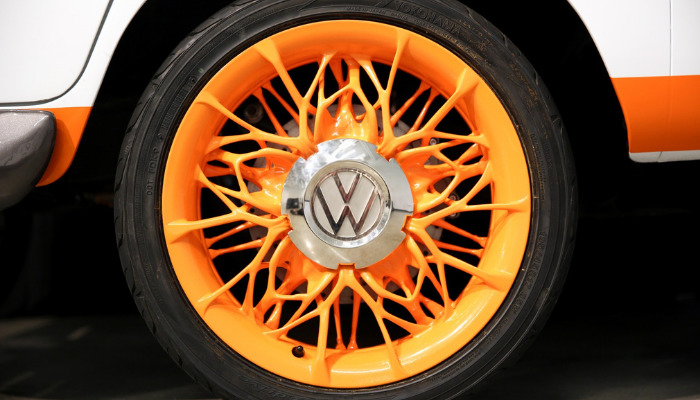
Autodesk generativna orodja za oblikovanje so pomagala oblikovati lažja kolesa na Volkswagnu 1962 tipa 2 z 11 okni.
Aditivna proizvodnja pomeni tudi večje možnosti personalizacije. Pravzaprav nekateri proizvajalci luksuznih avtomobilov že uporabljajo aditivno proizvodnjo za izdelavo modelov, prilagojenih zahtevam strank. Tradicionalne proizvodne metode, kot sta CNC ali brizganje, ne bi mogle dostaviti edinstvenih delov v konkurenčnih časih. Tudi stroški izdelave takšnih delov bi bili precej drugačni. Poleg tega se lahko personalizacija uporablja tudi za dobavo rezervnih delov, na primer za popravilo starejših modelov avtomobilov.
Primer končne uporabe je Fordov 3D-natisnjen vstopni razdelilnik iz aluminija (del motorja, ki dovaja mešanico goriva in zraka v jeklenke), ki je bil nameščen v Hoonitrucku iz leta 1977. Po navedbah proizvajalca je bil ta nadomestni del največji 3D-natisnjen avtomobilski del doslej. Tisk z uporabo naprave Concept Laser X LINE 2000R podjetja GE Additive je trajalo pet dni. Zgodovinsko gledano je Ford eno od podjetij, ki je opravilo največ raziskav o industrializaciji aditivne proizvodnje. Leta 1986 so investirali v SLA 3 (prvi 3D-tiskalnik, ki je bil kdaj izdelan). Družba je v uradnem sporočilu za javnost izjavila: “Ni trajalo dolgo, da bi ugotovili, da bi lahko izum uporabili za hitrejše in učinkovitejše ustvarjanje novih prototipnih modelov, kot kdaj koli prej.” Danes je podjetje natisnilo več kot 500.000 delov in “prihranilo milijarde dolarjev in milijone ur dela”. V svojem naprednem proizvodnem centru v Detroitu vlagajo v FDM, SLS 3D-tiskalnike in tiste za peskanje.
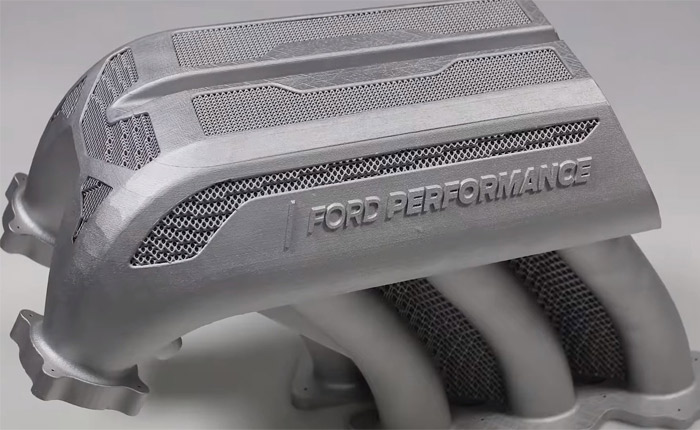
Fordov 3D-natisnjen vstopni razdelilnik iz aluminija | Vir fotografije: Ford
Drug primer je BMW Group, ki je leta 2020 odprl kampus aditivnE proizvodnje, nedaleč od Münchna. Gradnja kampusa je stala približno 15 milijonov evrov. Danes upravlja okoli 50 industrijskih sistemov za predelavo kovin in plastike. Proizvodnja prototipov, serijskih delov, raziskave in razvoj ter pridruženo usposabljanje v proizvodnji brez orodja potekajo na mestu. Ta naložba dokazuje zaupanje skupine BMW v tehnologije 3D-tiska. Tako kot drugi proizvajalci avtomobilov je skupina leta 1991 prvotno vlagala v aditivno proizvodnjo za izdelavo prototipov konceptnih avtomobilov. Kasneje so med drugim izdelali majhne serije delov za dirkalnike DTM, Rolls-Royce Phantom, BMW i8 Roadster in MINI. V enem letu je bilo 3D-natisnjenih 300.000 delov. Član uprave, Milan Nedeljković, je komentiral: »Aditivna proizvodnja je že sestavni del našega svetovnega proizvodnega sistema in je uveljavljen del naše strategije digitalizacije. V prihodnosti bodo nove tovrstne tehnologije pospešile proizvodnjo in nam omogočile, da še bolj izkoristimo potencial proizvodnje brez orodij. “
Dobavna veriga se spreminja
Deloitteova študija tudi poudarja, da bodo zgoraj omenjene spremembe na koncu vplivale na dobavne verige. Danes proizvajalci originalne opreme večino svojih delov oddajo zunanjim izvajalcem; poročilo pojasnjuje: »Ko bodo proizvajalci originalne opreme sprejeli pot razvoja izdelkov, bo končni rezultat dvojen: krajše dobavne verige in večji prispevek vrednosti proizvajalcev originalne opreme. Pomemben učinek aditivne proizvodnje lahko skrajša in poenostavi ogromne avtomobilske dobavne verige, ki trenutno delujejo. Proizvajalci originalne opreme sodelujejo s tisoči dobaviteljev pri iskanju različnih sestavnih delov v avtomobilih in nenehno iščejo načine za skrajšanje svojih dobavnih verig. ” Zato lahko podjetja izkoristijo aditivno proizvodnjo za preoblikovanje dobavnih verig s proizvodnjo na kraju samem in zmanjšanjem zalog delov.
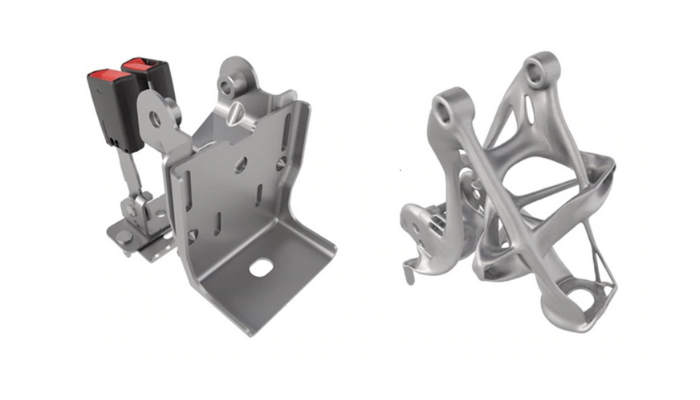
S pomočjo generativnega oblikovanja in aditivne proizvodnje je General Motor uspelo združiti osem različnih sestavnih delov nosilca sedeža v en sam 3D-natisnjen del.
Razvoj materialov
Z leti so izboljšave v tehnologiji materialov omogočile, da je več materialov kvalificiranih za proces aditivne proizvodnje. Avtomobilski deli so običajno izdelani iz visokozmogljivih polimerov, termoplastov, ojačanih z ogljikovimi vlakni in kovin. Proizvajalci originalne opreme so si aktivno prizadevali, da bi v karoserijo vozila vključili lažje materiale, kot so ogljikova vlakna in aluminij. Zato lahko materiali, prilagojeni za aditivno proizvodnjo, omogočijo vključitev več lastnosti v končne izdelke, vendar so ključnega pomena tudi pri razvoju funkcionalnih prototipov.
BASF Forward AM na primer sodeluje s svojimi strankami in proizvajalci strojne opreme pri razvoju inovativnih izdelkov z implementacijo aditivne proizvodnje. Forward AM je skupaj z Daimlerjem oblikoval nov nosilec motorja za zmanjšanje prenosa vibracij, s čimer so povečali udobje potnikov. Nosilec motorja je v zadnjem desetletju večinoma izdelan iz polimernih materialov, ojačanih z vlakni. Vendar pa je potreba po krajših razvojnih ciklih in nižjih stroških ta tradicionalni proces oblikovanja in materialov postavila pod pritisk. BASF Forward AM je z vsako spremembo zasnove odpravil zelo drage zahteve po novih kalupih z vključitvijo tehnologij aditivne proizvodnje v procesu. Izziv je bil naslednji: izpolniti stroge zahteve glede toplotnih in mehanskih lastnosti v preskusnih pogojih. Potrebovali so zelo tog in toplotno stabilen material. Popolnoma se je ujemal Ultrasint PA6 MF (mineralno polnjen poliamid 6, ki je boljši od PA11 in PA12), s katerim so izdelali prototipe, pripravljene za preskušanje, v manj kot 48 urah (namesto v nekaj tednih z brizganjem). Čeprav je bila zasnova 3D-natisnjenega dela videti drugače, bi jo lahko kot izvirnik uporabili za popolnoma funkcionalen prototip v fazi razvoja, ko ni bilo na voljo nobenega dela za brizganje. Ključno je bilo najti pravo zamenjavo materiala za reprodukcijo brizganega dela.
Kakšna je prihodnost avtomobilskih aplikacij aditivne proizvodnje?
V zadnjih letih so morali proizvajalci avtomobilov raziskati nove poslovne modele, da bi dosegli rast. V Jabilinem poročilu o trendih avtomobilske industrije lahko preberete, da ima 71 % avtomobilskih podjetij časovni okvir za izhod na trg, krajši od 2 let. Mnogi si prizadevajo za nove tehnologije, vključno z aditivno proizvodnjo, da bi ohranili kratke razvojne cikle in dosegli nižje stroške. Zanimiva je tudi elektrifikacija vozil, saj si želi približno 50 % avtomobilskih proizvajalcev v bližnji prihodnosti postati vodilni na trgu popolnoma električnih vozil (EV). Ko se industrija oddaljuje od motorjev z notranjim zgorevanjem, se 3D-tisk pojavlja kot rešitev, ki lahko pospeši razvoj lažjih delov za električna vozila. Lahka teža je ključnega pomena za električna vozila, saj neposredno vpliva na čas delovanja baterije.
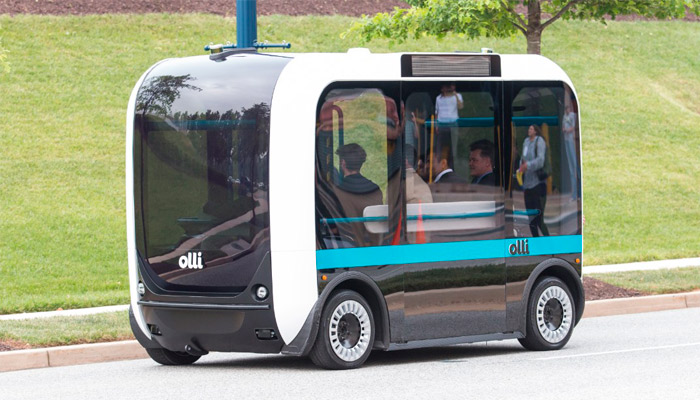
V sektorju električnih vozil ste morda že slišali za Ollija, 3D-natisnjeni avtonomni električni minibus, ki ga je leta 2016 oblikoval Local Motors. Proizvajalec trdi, da je bilo približno 80 % delov 3D-natisnjenih, kar je skrajšalo celoten čas proizvodnje za 90 %. Hitrost je omejena na 40 km/h, zaradi česar je Olli primeren za mestna središča, univerzitetne šole in bolnišnice. Pred tem je Local Motors predstavil roadster Strati, električnega dvoseda, ki vsebuje 75 % 3D-natisnjenih delov.
Poleg tega, z naraščanjem povpraševanja po povezanih vozilih narašča, se povečuje tudi potreba po elektronskih napravah, kot so senzorji in antene v vozilu. S tem povečanjem prihaja tudi do večje potrebe po oblikovanju in proizvodnji manjše, bolj zapletene elektronike. Na podlagi tehnologij 3D-tiska mikro in nano merilih je mogoče interno oblikovati bolj zapletene elektronske komponente, ki jih je mogoče neposredno vgraditi v vozilo. 3D-tisk lahko zmanjša stroške in čas razvoja za ustvarjanje teh naprav.
Kot smo že omenili, prilagajanje ponuja številne možnosti. Na primer, stranke MINI imajo trenutno možnost prilagoditi svoja vozila z oblikovanjem stranskega pasu na sovoznikovi strani v kabini in stranskih vložkov. BMW group je v svojih različnih projektih 3D-natisnil več kot 140.000 komponent. Christian Reinhardt, ki je del BASF Forward AM od leta 2019, je komentiral: »Po mojem mnenju je bila ena najbolj vznemirljivih in pomembnih aplikacij projekt MINI” Your Customized “. Ta projekt je pokazal, da je v resničnem serijskem avtomobilu mogoče imeti 3D-natisnjen del in da bi lahko individualizacija po meri kupca dodala vrednost, ki je še nikoli nismo videli. Prepričan sem, da bo ta projekt postal pionir številnih aplikacij, ki prihajajo. “
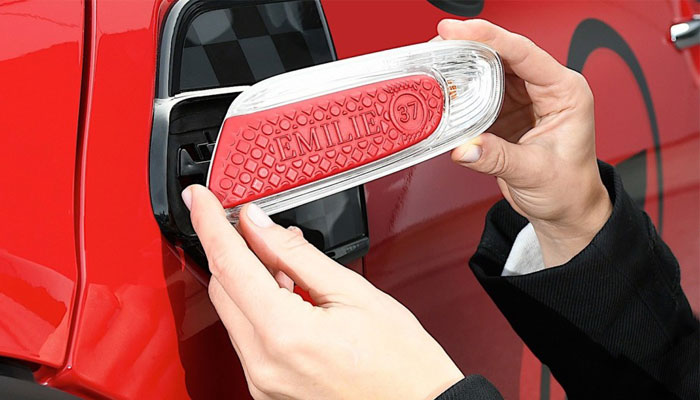
Zahvaljujoč 3D-tisku lahko MINI-ja stranke prilagodijo.
Globalno gledano skoraj vsi akterji na trgu vlagajo v tehnologije 3D-tiska, da bi prešli v proizvodnjo bolj zapletenih in visoko zmogljivih delov. Generalni direktor General Motors, direktor aditivnega oblikovanja in proizvodnje Kevin Quinn, pojasnjuje: »V povprečju je v vsakem vozilu 30.000 delov. Ne želimo natisniti vseh 30.000 kosov. Namesto tega smo zelo realni. Osredotočeni smo na proizvodne priložnosti, kjer lahko zagotovimo poslovno vrednost za GM in za stranke. “
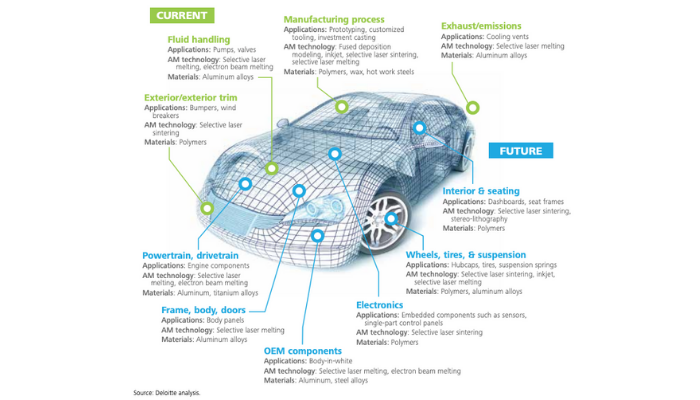
Sedanje in prihodnje aplikacije iz Deloittove študije. | Vir slike: Deloitte Analysis
Zato proizvajalci originalne opreme za povečanje splošnih proizvodnih zmogljivosti in zmanjšanje stroškov, kar je bila glavna aplikacija sektorja, začenjajo izkoriščati aditivno proizvodnjo za ustvarjanje novih izdelkov in omogočanje preoblikovanja dobavne verige.
Vir: 3dnatives.com